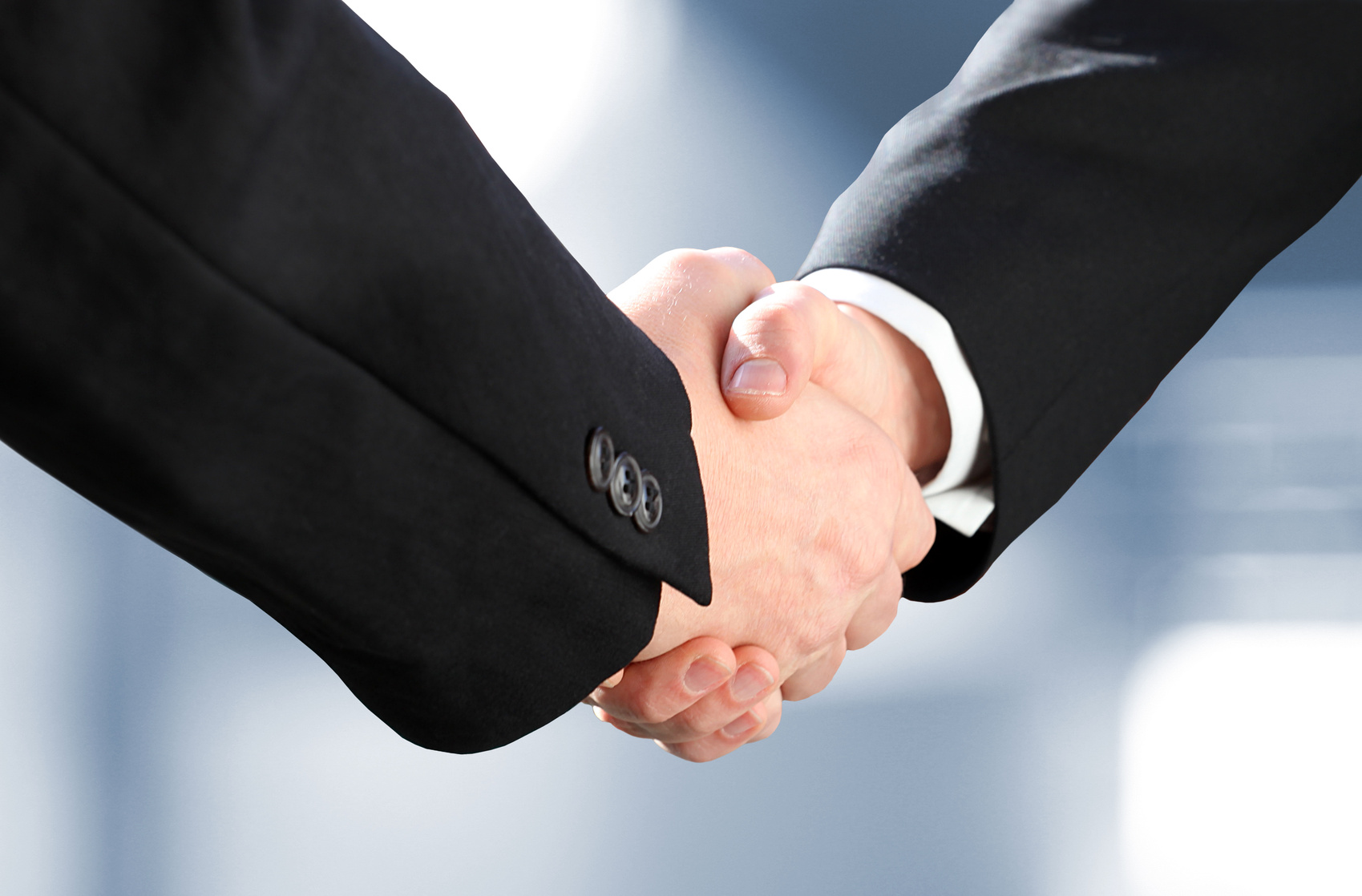

Here we've listed a few clients, but this is a partial client list since the our privacy policy prohibits their institution's name from being presented on this client list.
- ABB
- ACQUA ENGINEERING
- ACS DOBFA
- AGIP
- AUSY
- BAYER
- CELLULOSA 2000
- CELLULOSA CALABRA
- COMER
- COPRIM
- ENI
- ENI REFINING & MARKETING
- ENIPOWER
- FLENCO
- GICOTECNICA
- SANMARCO
- SARL RABIE INDUSTRIE
- SIMECO
- SIMENS
- SNAMPROGETTI
- SONATRACH
- STB ENGINEERING
- SUN PAPER INDUSTRY
- TECHNIP
- TECNIMONT
- TECNOLAB
- KARACHAGANAK
- KOGON REMSTROYKOMPLEKT
- MAUL BELSER
- MULTISERVICE
- PLOIMERI EUROPA
- POLYMERLATEX
- POM LTD
- PRISMA
- PROGECO
- S.N.C.P.A
- S.N.G.N. ROMGAZ
- SAIPEM
OUR MAIN EXPERIENCES:
The client is a private company. IPS was contracted to perform a retrofitting design of existing batch process to increasing production. The revamping project based on the use of Reactive distillation concept in the existing plant.
The following project tasks were executed:
- Process design basis development;
- Process simulation;
- Process flow diagrams (PFDs) and P&ID;
- Equipment, Machinery and Instruments DS & MR;
- Main equipment construction drawings.
The client was a private company in EU that manufactures a range of oleochemical decided to increasing their manufacturing with the addition of a new Fatty acid fractionation in order to obtaion pure fatty acids (30 TPD) for new derivatives from it. IPS was asked to develop Front End Engineering and generated a preliminary cost estimation.
The following project tasks were executed:
- Process design basis development
- Process simulation
- Process flow diagrams (PFDs) and P&ID
- Capital cost estimate development
- Raw material, finished product and utility requirement mass balances
- Equipment, Machinery and Instruments DS & MR
- Propertary equipment construction drawings.
The client, an producer of acetate esters contracted IPS to execute a new waste water treatment project in order to reduce effluent contaminants in accordance to local laws.
The conceptual and basic design were based on the use of Membrane Bioreactor (MBR). Project tasks included:
- Process design basis development;
- Mass and energy balance model preparation;
- Process design, and process flow diagram (PFD) and process description preparation;
- Equipment layout drawings preparation
- Detailed equipment specifications preparation
- Capital, operating, and annual cost estimates development.
IPS Engineering (IPS) was contracted by the client, a start-up technology company, to develop a simulation for a process that produces diesel from corn oil using a hydrotreater, hydrocracker, and distillation unit. The simulation also included a hydrogen reformer and hydrogen recycle loop. Pressure swing adsorption (PSA) was included for hydrogen purification along with hydrogen membrane separation technology. A distillation train was modeled to fractionate the diesel from light gases and propane produced from cracking triglycerides. The product is termed “Green Diesel” because the feedstock source may be edible oil, waste grease, or biomass.
This new production rate was compared to the original design documents which were supplied by the client.
Design calculations were verified to determine the adequacy of the existing unit when the additional production were added. IPS also suggested the next actions that are recommended to develop the present analysis with the scope to verify the realistic production level that can be reached.